
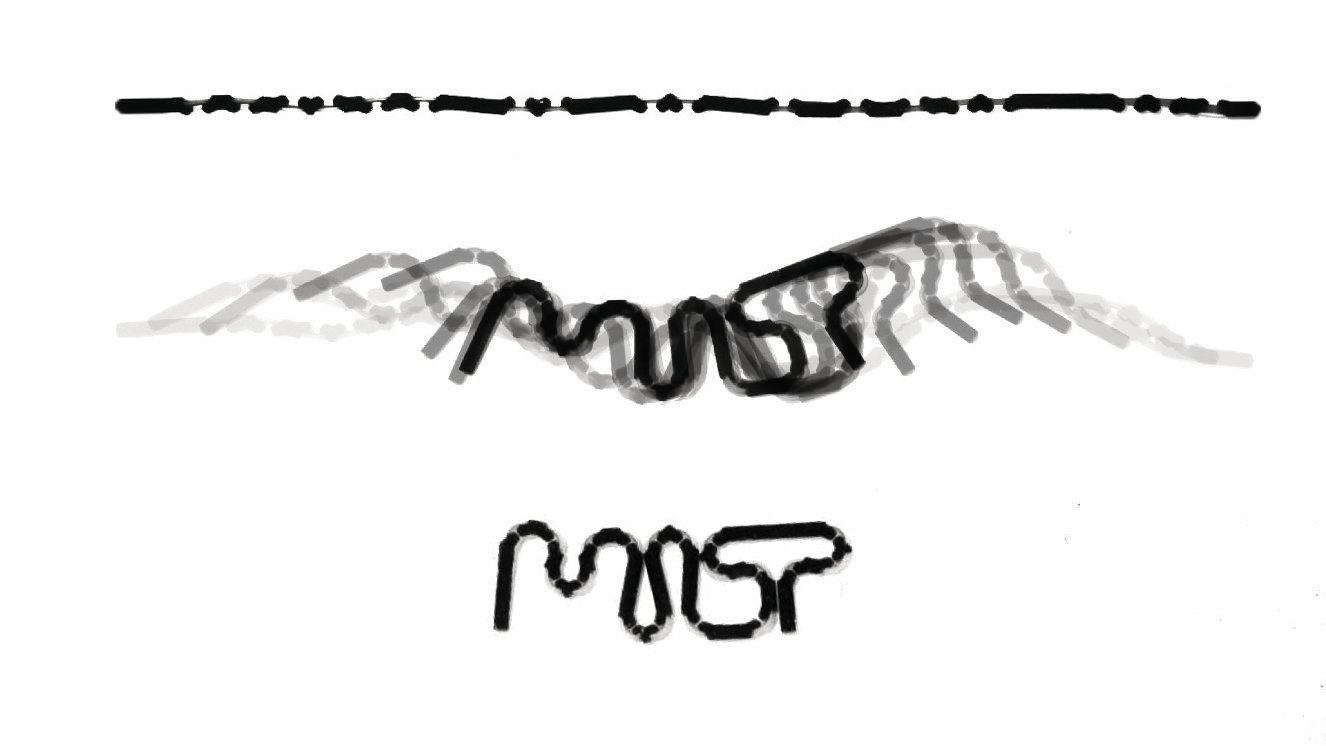
“We can thus harness this incompatibility and design structures that can dramatically change in shape.”įor multiple polymers, their property-structure-processing relationships can be very complicated and very material-specific. “When two or more materials that respond differently to environmental stimuli are combined together into a composite material, there will be some incompatibility in the structure,” Qi says. Composites can offer significantly improved physical properties and greater functionality, compared to single materials.

Using his printer and a special composite material made from acrylic and epoxy, Qi successfully 4D-printed objects that transformed shape up to 90 percent faster than previously possible because the tedious mechanical programming steps were already integrated into the 3D printing process. It can make products from a variety of materials including hydrogels, conductive inks, elastomers, and shape memory polymers, which can be programmed to "remember" a shape and then transform into it when heated to a certain temperature. Qi’s printer combines four different printing technologies: aerosol, inkjet, direct ink write, and fused deposition modeling. Jerry Qi, Georgia Institute of Technology How It Works The m4 3D printer is a very powerful 3D printing system that integrates four printing methods into one single platform. Their paper about the technology was recently published in ScienceDaily. The researchers envision it being used for a variety of applications in such industries as aerospace and medicine. “It is a very powerful 3D printing system that integrates four printing methods into one single platform, which enables the efficient printing of complicated parts that can change shape, thus expanding future printing applications.” “We call it the multi-material multi-method 3D printer,” Qi says. Glaucio Paulino (left) and Jerry Qi lead a team of researchers that has developed a way to use 3D printers to create objects that expand dramatically. But a research team led by Jerry Qi, a mechanical engineering professor at Georgia Institute of Technology, along with scientists at the Singapore University of Technology and Design, have developed a powerful new 4D printer that can create self-assembling 4D-structures much more quickly and efficiently.įor You: The latest in manufacturing and design breakthroughs Also, most commercial printers can only print 4D using a single material, which greatly limits design choices. Although 4D printing is still an emerging field, it has huge potential for expanding engineering design.Ĭurrently 4D printing requires complex and time-consuming post-processing steps to mechanically program each component. This ability depends on the development and use of unique programmable materials. Thus, the “fourth dimension” is, literally, transformation. “4D” printing is an emerging technology that 3D-prints solid components programmed to change into other shapes when certain environmental parameters - temperature, light, and humidity – are reached.
